Knife gate valve
SLV
Compact push through slurry knife gate valve
Available size range:
DN 50 - DN 900 (2” - 36”).
Product data sheet:
Discover more
About SLV
Stafsjö’s SLV is a push through slurry knife gate valve with superior flow characteristics, offering reliable and bi-directional shut-off performance in abrasive and demanding mineral processing applications.
The SLV valve is modular designed and it can easily be customized with actuators and related automation accessories to different process conditions. The valve is also available with mechanical lock out. As standard, the SLV is supplied with a robust and precision machined nodular iron valve body and strong duplex stainless steel gate, which is also special grinded with purpose of reducing the friction when it cycles through the valve’s rubber seats.
In addition to this slurry valve Stafsjö also offers a fully flanged slurry valve, the SLF, and two high pressure versions, the SLH and SLX, available in pressure rating up to 50 bar.
Download the product data sheet for additional technical information.
Specifications
Shut-off technique
Bi-directional
Push-through
Valve seat material
EPDM
Natural rubber
Connection type
Wafer/Semi lugged
Valve body material
Nodular iron
Industries
Mining
Power
Steel
Product features
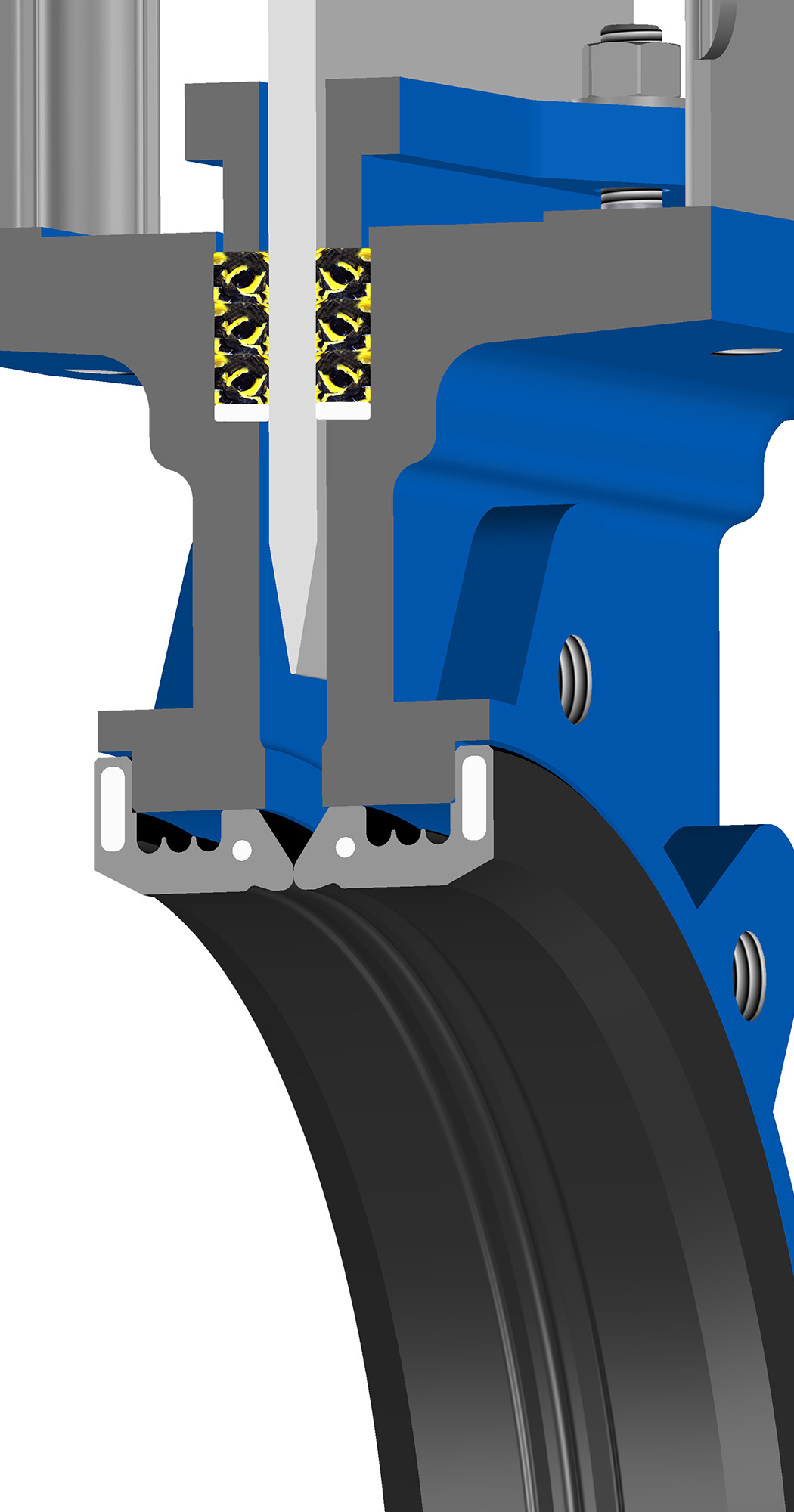
A precise gate alignment extend the service life
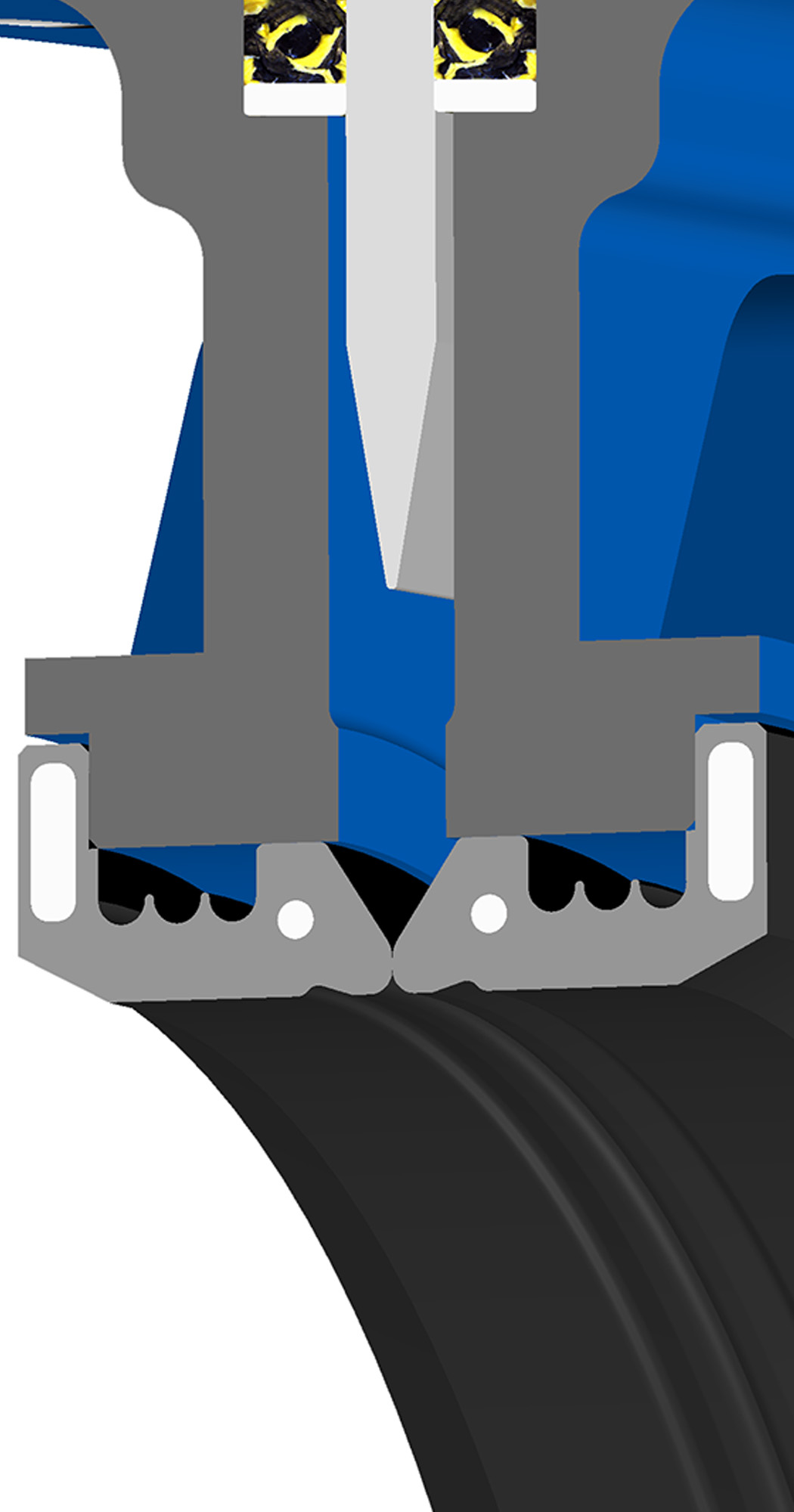
Reinforcements rings ensure stability and performance
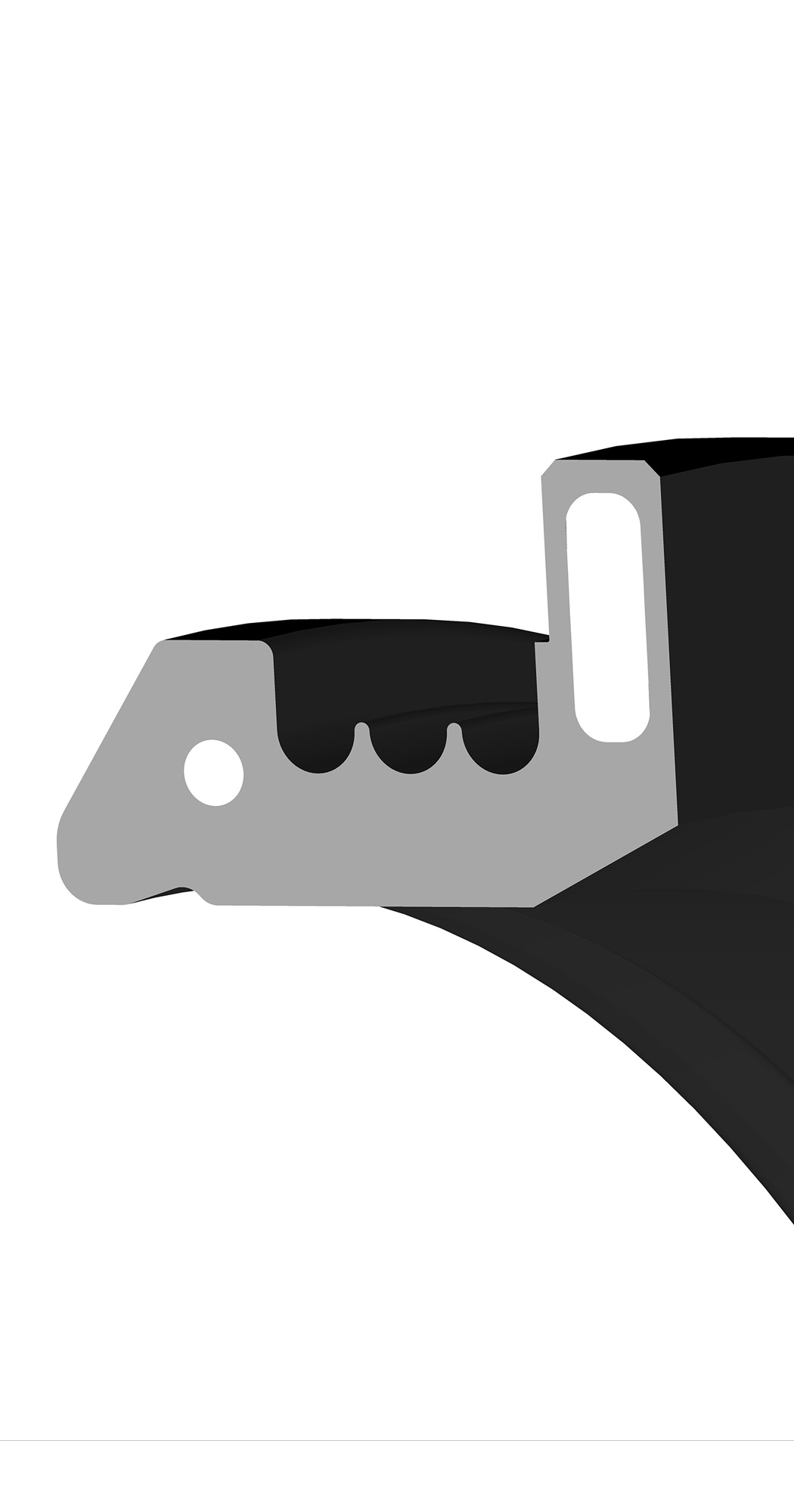
Expansion areas reduce stress and actuation force
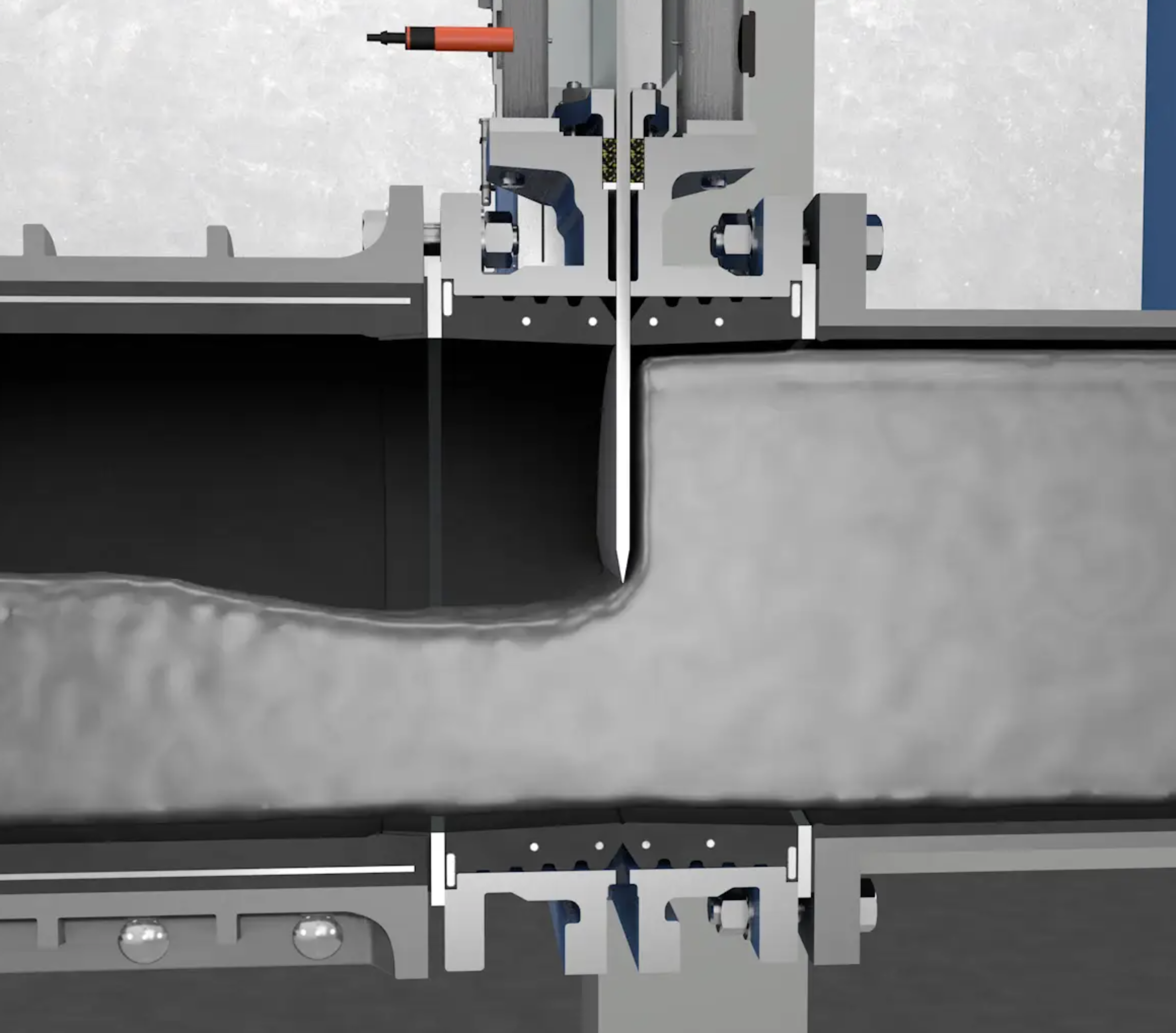
Downloads
- Title Format Size Restriction
-
Knife gate valve SLV
PDF 1 MB
- Title Format Size Restriction
-
Manual actuators
PDF 2 MB -
Double acting pneumatic cylinder SC
PDF 1 MB -
Hydraulic cylinder
PDF 2 MB -
Electric motor LINAK
PDF 1 MB -
Electric motor AUMA
PDF 91 KB -
Stafsjö standard accessories
PDF 4 MB
- Title Format Size Restriction
-
Knife gate valve specification guide
PDF 5 MB
- Title Format Size Restriction
-
Installation and service instruction
PDF 4 MB -
Maintenance instruction for SLV, SLF, SLH and SLX
PDF 380 KB