Troubleshooting
Sometimes the knife gate valve does not work as intended. There can be several sources to the problem. This troubleshooting guide is a tool to find out what is causing the problem and we also provide recommendations on actions to solve it. Our valve experts at Stafsjö and all around the world are also ready to support you.
Discover more
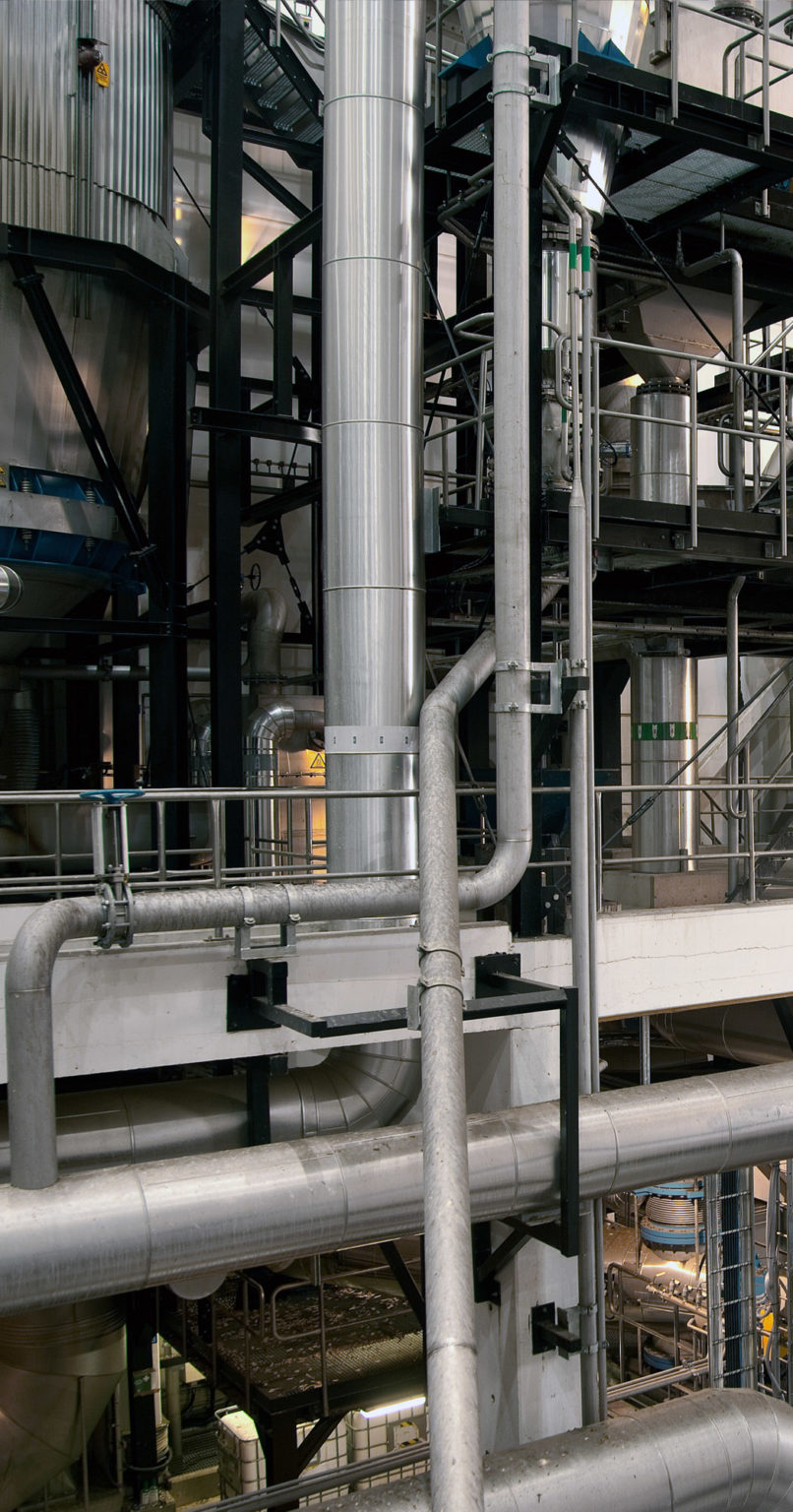
Troubleshooting
- Inspect the knife gate valves on regular basis for any leakages. Seat and box packing are wear parts that have to be replaced regularly. The interval for both inspection and replacement depends on the application and operating data such as pressure, temperature, erosion, chemical, mechanical effect of the media on the materials in the knife gate valve and on how often the valve is operated.
- A threaded stem is used on hand wheel, bevel gear and electric operated valves to open/close the valve. The stem is greased upon delivery – make sure to grease it on regular basis.
Media, pressure, temperature and operating intervals affect the box packing braids in different ways.
- Observe safety instruction in installation and service instruction and plant specific safety instructions before any work begins. Media leakage can seriously harm personnel.
- Begin to re-tighten the nuts on top of the gland crosswise bit by bit according torques given in the installation and service instruction. Do not tighten more than necessary. It can damage the stuffing box braids and make the valve heavy to operate.
- If possible, cycle the valve a few times and re-tighten if leakage does not stop. Also inspect the gate for scratches. If it is worn, the stuffing box ability to seal tight is affected.
- If the gate is worn or the stuffing box leakage does not stop after the nuts have been re-tightened, prepare the valve for maintenance. Stafsjö can submit maintenance instructions as support.
Stafsjö can supply original spare parts to your valve. Each valve is marked with a label including the valve’s article and serial number. With this info we can ensure you receive correct spare parts to your valve. Request your original spare parts from xxx and we turn back with a proposal.
The reason can be an outcome of one or several of reasons below.
- Process conditions exceed design limits of the valve
- Valve is clogged
- Damaged seat or gate
- Wrongly installed or error in actuator
- Wrongly installed or error in limit switches
- Not enough air supply pressure
- Not enough air flow supply
- Begin to verify that the process conditions does not exceed design limits of the valve. Pay special attention to pressure, pressure ratio, temperature and media characteristics vs. the valve specification. See product data sheet for design limits of the valve. Each valve is also marked with its pressure limits. Observe that some knife gate valves are uni-directional while others can operate independent of pressure direction.
- If process allows, we recommend cycling the knife gate valve open/close several times to exclude possibility something is jammed in between gate and seat preventing the valve to seal tight or close 100 %.
- Ensure the stroke length is correctly adjusted. On remote operated valves the clevis pin should be centred in the beam holes.
- If the valve does not provide a liquid or product tight sealing after the inspection, the seat and/or gate may be worn out and you should prepare the knife gate valve for maintenance.
Stafsjö can supply original spare parts to your valve. Each valve is marked with a label including the valve’s article and serial number. With this info we can ensure you receive correct spare parts to your valve. Request your original spare parts and we turn back with a proposal.
The leakage can be an outcome of one or several of reasons below.
- Wrong length of bolts in flanges
- Loose flange bolting
- Valve not centred at flange connection
- Valve not parallel to flanges
- Gasket not centred
- Wrong gasket material
- For length and size of flange bolts, see each product data sheet. Don’t forget to consider depth of flanges, washers and gaskets when calculating bolt lengths. Some of Stafsjö’s valves already have integrated gaskets and doesn’t require additional ones.
- Follow the step by step instruction in the installation and service instruction for the knife gate valve. Pay attention to valve type specific instructions.
The reason can be an outcome of one or several of reasons below.
- Process conditions exceed design limits of the valve
- Valve is clogged
- Damaged seat or gate
- Wrongly installed or error in actuator
- Wrongly installed or error in limit switches
- Not enough air supply pressure
- Not enough air flow supply
- Begin to verify that the process conditions does not exceed design limits of the valve. Pay special attention to pressure, pressure ratio, temperature and media characteristics vs. the valve specification. See product data sheet for design limits of the valve. Each valve is also marked with its pressure limits. Observe that some knife gate valves are uni-directional while others can operate independent of pressure direction.
- If process allows, we recommend cycling the knife gate valve to exclude possibility something is jammed in between gate and seat preventing the valve to seal tight or close 100 %.
- Verify external components such as limit switches and actuators operate as intended, receive signal and is installed correctly. Observe safety instruction in installation and service instruction and plant specific safety instructions before any inspection begins. Stafsjö can support with installation and service instruction for each component.
- Ensure the stroke length is correctly adjusted. On remote operated valves the clevis pin should be centred in the beam holes.
- Measure air supply pressure at the actuator ports. Pneumatic operated valves are as standard intended to operate with within 5-10 bar air supply. Operating the knife gate valve with air pressure below 5 bar normally require an oversized actuator to ensure force to operate the valve in a smooth movement to its full open/closed position.
- The pipework for the compressed air supply to the cylinder should be at least the same size as the air connections on the pneumatic cylinder, i.e. ¼” or ½”. Long feed lines may require oversized pipe works. For detailed information on pipe size, see installation and service instruction for the pneumatic cylinder.
- If no external defect is observed, we recommend preparing the valve for full inspection and maintenance.
Stafsjö can supply original spare parts to your valve. Each valve is marked with a label including the valve’s article and serial number. With this info we can ensure you receive correct spare parts to your valve. Request your original spare parts and we turn back with a proposal.
The reason can be an outcome of one or several of reasons below.
- Process conditions exceed design limits of the valve
- Valve is clogged
- Damaged seat or gate
- Too tightened gland
- Wrongly installed or error in actuator or accessories
- Not enough air supply pressure
- Not enough air flow supply
- Begin to verify that the process conditions does not exceed design limits of the valve. Pay special attention to pressure, pressure ratio, temperature and media characteristics vs. the valve specification. See product data sheet for design limits of the valve. Each valve is also marked with its pressure limits. Observe that some knife gate valves are uni-directional while others can operate independent of pressure direction.
- If process allows, we recommend cycling the knife gate valve to exclude possibility something is jammed in between gate and seat preventing the valve to operate smoothly.
- Verify gland is not tightened too much. Check gland nuts torques. If they are too tightened and the gland horizontal flat surface is close to meet the top surface of the body, it has most likely been re-tightened before because of leakage. We recommend preparing the valve for full inspection and maintenance.
- Verify external components such as limit switches, solenoid valves and actuators operate as intended, receive signal and is installed correctly. Observe safety instruction in installation and service instruction and plant specific safety instructions before any inspection begins. Stafsjö can support with installation and service instruction for each component.
- Measure air supply pressure at the actuator ports. Pneumatic operated valves are intended to operate with within 5-10 bar air supply. Operating the knife gate valve with air pressure below 5 bar normally require an oversized actuator to ensure force to operate the valve in a smooth movement to its full open/closed position.
- The pipework for the compressed air supply to the cylinder should be at least the same size as the air connections on the pneumatic cylinder, i.e. ¼” or ½”. Long feed lines may require oversized pipe works. For detailed information on pipe size, see installation and service instruction for the pneumatic cylinder.
If no external defect is observed, we recommend preparing the valve for full inspection and maintenance. Stafsjö can supply original spare parts to your valve. Each valve is marked with a label including the valve’s article and serial number. With this info we can ensure you receive correct spare parts to your valve. Request your original spare parts and we turn back with a proposal.
The reason can be an outcome of one or several of reasons below.
- Process conditions exceed design limits of the valve
- Valve clogged
- Damaged seat or gate
- Gland nuts tightened by too high torque
- Begin to verify the process conditions does not exceed design limits of the valve. Pay special attention to pressure, pressure ratio, temperature and media characteristics vs. the valve specification. See product data sheet for design limits of the valve. Each valve is also marked with its pressure limits. Observe that some knife gate valves are uni-directional while others can operate independent of pressure direction.
- Observe safety instruction in installation and service instruction and plant specific safety instructions before any inspection work begins. Media leakage can seriously harm personnel.
- If process allows, we recommend cycling the knife gate valve to exclude possibility something is jammed in between gate and seat causing excessive force to operate the valve.
- Begin to check gland nuts torques. If they are too tightened and the gland horizontal flat surface is close to meet the top surface of the body, it has most likely been re-tightened before because of leakage. We recommend preparing the valve for full inspection and maintenance.
Stafsjö can supply original spare parts to your valve. Each valve is marked with a label including the valve’s article and serial number. With this info we can ensure you receive correct spare parts to your valve. Request your original spare parts and we turn back with a proposal.